Hot wire CNC foam cutter
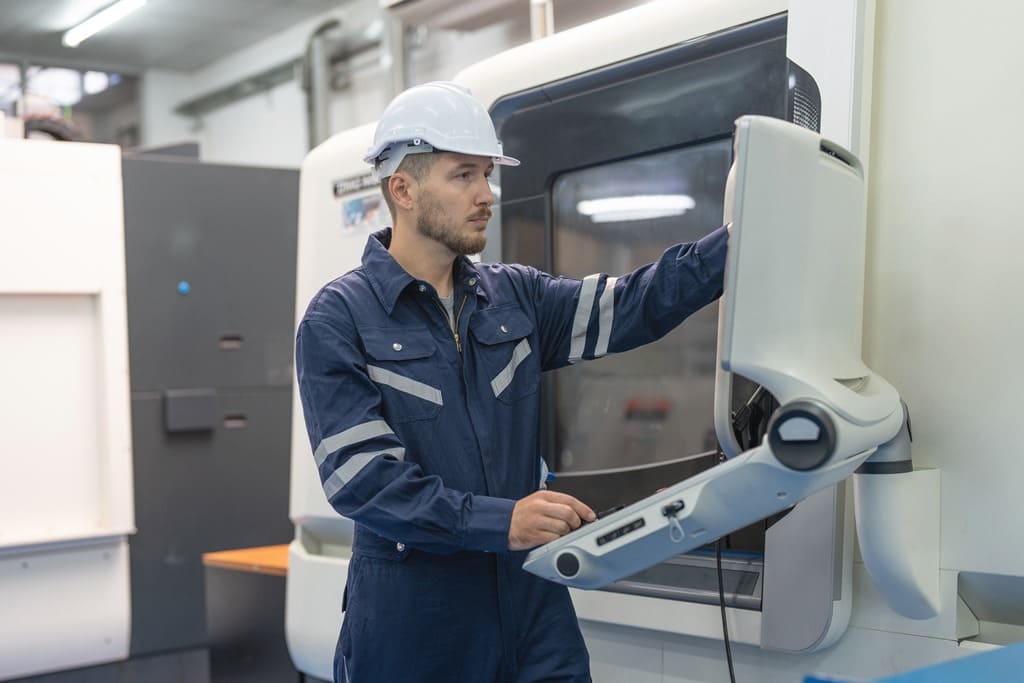
Are you interested in creating intricate designs out of foam? Look no further than a hot wire CNC foam cutter. This tool allows for precise cuts and shapes, making it a popular choice in various industries. In this article, we will cover everything you need to know about building your own hot wire CNC foam cutter, including the necessary materials and safety precautions. We’ll also provide tips and tricks for using your new tool effectively and explore its applications in different fields. Join us as we dive into the world of hot wire CNC foam cutters!
Materials Needed to Build a Hot Wire CNC Foam Cutter
Building a hot wire CNC foam cutter requires specific materials that are essential to the process. The first material you will need is a power supply, which can be either an old computer power supply or a dedicated 12V DC power supply. You will also need a stepper motor driver board, which controls the movement of the cutting wire. Additionally, you will need a microcontroller board such as an Arduino or Raspberry Pi to control the entire system.
The next set of materials needed for building your hot wire CNC foam cutter includes mechanical components such as linear bearings, threaded rods, and nuts. These components are used to create the frame and guide rails for the cutting wire. You will also need a hot wire cutter kit that includes nichrome wire and tensioners to hold it in place. Other necessary items include limit switches, wires, connectors, and heat shrink tubing.
Finally, you will need some basic tools such as pliers, screwdrivers, soldering iron, and heat gun to assemble all the parts together. It’s important to note that while some of these materials may be readily available at home or local hardware stores, others may require ordering online or from specialty suppliers. By gathering all these materials beforehand and following our step-by-step guide below on how to build your own hot wire CNC foam cutter, you’ll be able to create precise cuts on foam with ease.
Understanding the Basics of Hot Wire CNC Foam Cutters
Hot wire CNC foam cutters are an essential tool for many industries that require precise and accurate cutting of foam materials. These machines use a heated wire to slice through foam with ease, creating intricate shapes and designs that would be impossible to achieve by hand. Understanding the basics of how these machines work is crucial for anyone looking to build or use one.
The key component of a hot wire CNC foam cutter is the heated wire itself. This wire is typically made from nichrome, a type of resistance wire that can withstand high temperatures without breaking or degrading. When electricity is passed through the wire, it heats up and becomes hot enough to melt through foam materials. The wire is attached to a frame that can move in multiple directions, allowing it to cut complex shapes and angles with precision.
In addition to the heated wire, hot wire CNC foam cutters also require a control system that can accurately guide the movement of the cutting frame. This control system typically consists of software that allows users to design their cuts on a computer and then send those instructions to the machine. The machine then moves the cutting frame along those predetermined paths, ensuring that each cut is made exactly as intended.
Step-by-Step Guide to Building Your Own Hot Wire CNC Foam Cutter
Building your own hot wire CNC foam cutter can be a fun and rewarding project. Not only will you save money by building it yourself, but you’ll also have the satisfaction of knowing that you created something useful with your own two hands. Before you begin, make sure you have all the necessary materials on hand.
The first step in building your hot wire CNC foam cutter is to create a design plan. This will help you determine the size and shape of your machine, as well as the type of materials you’ll need. Once you have a plan in place, it’s time to start gathering your materials. You’ll need a power supply, stepper motors, linear bearings, threaded rods, and other components depending on your design.
Next, assemble the frame of your hot wire CNC foam cutter using aluminum extrusions or other sturdy materials. Install the stepper motors and linear bearings according to your design plan. Then attach the threaded rods and connect them to the stepper motors. Finally, install the hot wire cutting tool and connect it to a power source. Once everything is assembled and connected properly, test out your new machine by cutting some foam!
Hot wire CNC foam cutter is a type of computer numerical control (CNC) machine used for cutting foam, polystyrene, and other materials. The machine works by heating a wire to a high temperature and then using it to cut through the material. This technology is widely used in the construction industry for creating architectural models, insulation, and other applications.
Hot wire CNC foam cutter machines are highly accurate and efficient, making them an attractive option for businesses looking to improve their manufacturing processes. They are also easy to use, with many models featuring user-friendly interfaces and automated controls. Additionally, hot wire CNC foam cutter machines are capable of cutting intricate shapes and designs, making them ideal for creating custom products and prototypes.
Hot wire CNC foam cutter is a type of computer numerical control (CNC) machine that uses a heated wire to cut through foam, polystyrene, and other similar materials. The wire is heated to a high temperature, which melts the material as it cuts through it. This process is often used in the manufacture of architectural models, sculptures, and other types of three-dimensional objects.
The hot wire CNC foam cutter machine consists of a cutting table, a wire tensioning system, and a wire heating system. The cutting table is typically made of aluminum or steel and is designed to hold the material being cut in place. The wire tensioning system is used to keep the wire taut and in position during the cutting process. The wire heating system consists of a power supply, a transformer, and a wire that is heated by passing an electric current through it.
The cutting process begins by importing a 3D model into the machine’s software. The software then generates a toolpath that the machine follows to cut the material. The wire is guided along the toolpath by the machine’s cutting head, which moves in three axes: X, Y, and Z.
Hot wire CNC foam cutter machines are capable of cutting complex shapes quickly and accurately. They are also very versatile, as they can be used to cut a wide variety of materials, including foam, polystyrene, and even some types of plastic. However, they are not suitable for cutting hard materials such as metal or wood.
Overall, hot wire CNC foam cutter machines are a valuable tool for anyone involved in the creation of three-dimensional objects. They offer a high level of precision and speed, and their versatility makes them ideal for a wide range of applications.
The cutting wire is the most important component of a hot wire CNC foam cutter machine. It is responsible for cutting the material with precision and accuracy. The wire is made of a special alloy that can withstand high temperatures. The thickness of the wire depends on the material being cut and the desired precision. Generally, a thinner wire is used for more intricate cuts. The wire is held in place by a wire tensioning system that ensures it remains taut during the cutting process.
The machine frame is the backbone of a hot wire CNC foam cutter machine. It provides the necessary rigidity and stability for the cutting wire to move smoothly and accurately. The frame is typically made of aluminum or steel and is designed to be lightweight yet sturdy. The size of the frame depends on the size of the material being cut. A larger frame is required for cutting larger materials.
The control system is the brain of the hot wire CNC foam cutter machine. It is responsible for controlling the movement of the cutting wire and ensuring that the cuts are accurate and precise. The control system consists of a computer, software, and electronic components. The software is used to create the cutting path and send the instructions to the machine. The electronic components are responsible for translating these instructions into movement of the cutting wire.
In conclusion, the cutting wire, machine frame, and control system are the three main components of a hot wire CNC foam cutter machine. Each component plays a critical role in ensuring that the machine can cut materials with precision and accuracy. By understanding these components, one can better appreciate the complexity and sophistication of hot wire CNC foam cutter machines.
Safety Precautions to Take When Using Hot Wire CNC Foam Cutters
When using a hot wire CNC foam cutter, it is important to take certain safety precautions to avoid accidents and injuries. First and foremost, always wear protective gear such as gloves and eye goggles when operating the machine. The hot wire can cause serious burns if it comes into contact with skin, so it is crucial to handle it with care.
Another important safety measure is to ensure that the work area is well-ventilated. When cutting foam, fumes are released which can be harmful if inhaled in large quantities. Make sure that there is adequate airflow in the room or use a ventilation system to remove any harmful particles from the air.
It is also essential to keep children and pets away from the machine while it is in operation. The hot wire can cause serious harm if touched accidentally, so it’s best to keep curious hands and paws at a safe distance. Additionally, never leave the machine unattended while it’s running - always stay nearby in case of any issues or emergencies.
Tips and Tricks for Using Your Hot Wire CNC Foam Cutter
Once you have built your own hot wire CNC foam cutter, it’s time to start using it for your projects. Here are some tips and tricks to help you get the most out of your machine:
Firstly, make sure that you have the right type of wire for the job. Different types of foam require different types of wires, so be sure to do your research before starting a project. You should also ensure that the wire is properly tensioned and straight before cutting, as this will help to produce clean and accurate cuts.
Another important tip is to take your time when cutting. Rushing through a project can lead to mistakes and uneven cuts, which can ruin the final product. Instead, take your time and move the wire slowly through the foam, making small adjustments as needed. This will help you achieve precise cuts every time.
Applications of Hot Wire CNC Foam Cutters in Various Industries
Hot wire CNC foam cutters have a wide range of applications in various industries. One of the most common uses is in the construction industry, where they are used to create architectural models and prototypes. These machines can quickly and accurately cut foam blocks into any shape or size required for building models of buildings, bridges, and other structures. This allows architects and engineers to test their designs before construction begins, saving time and money in the long run.
Another industry that benefits greatly from hot wire CNC foam cutters is the packaging industry. Foam inserts are commonly used to protect fragile items during shipping, and these machines can quickly produce custom inserts that fit perfectly around any item. This ensures that products arrive at their destination undamaged, reducing returns and increasing customer satisfaction.
The entertainment industry also makes use of hot wire CNC foam cutters to create props and set pieces for movies, TV shows, and theater productions. These machines can easily carve intricate shapes out of foam blocks, allowing designers to bring their visions to life with ease. From giant dragons to realistic rocks, hot wire CNC foam cutters are an essential tool for creating immersive environments on stage or screen.
Autor: Materiał partnera